Smarter Demolition by Design: Why Innovation Led the Way at Kalamia Sugar Mill
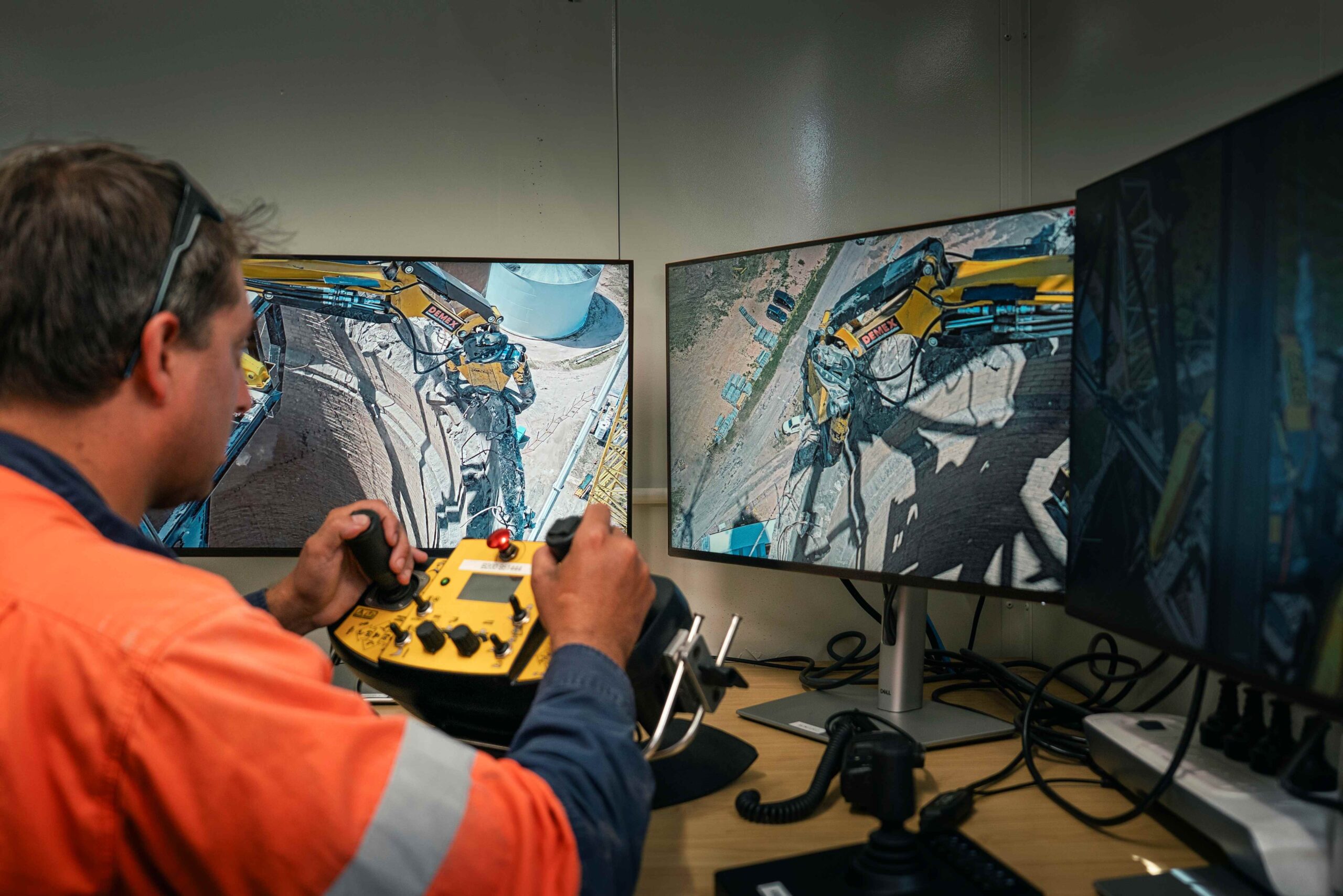
Demolition isn’t one-size-fits-all, especially when you’re dealing with towering industrial structures, live operational environments, and tight timeframes. At DEMEX, innovation is a deliberate choice driven by the unique demands of each project.Â
This thinking shaped our approach at the Kalamia Sugar Mill, where we demolished two deteriorating boiler stacks under complex and high-risk conditions. Facing extreme weather, structural instability, a live adjacent boiler house, and a tight deadline, the project demanded a solution that was both highly controlled and carefully engineered. We leaned into robotics and in-house design to deliver a tailored, safe, and efficient outcome.Â
Why Innovation Was EssentialÂ
From the outset, our early involvement with the client made their priorities clear: they needed a demolition partner who could deliver safely, with precision, and no delays, without impacting adjacent operations.Â
However, the site presented several non-negotiable constraints:Â
- The stacks were deteriorating and unsafe for conventional manual dismantling.Â
- Their proximity to a live and sensitive boiler house meant zero margin for error.Â
- A narrow window between sugar crushing seasons meant we had just weeks to complete the work.Â
- The extreme North Queensland summer brought challenges like cyclonic rain, flooding, and intense heat.Â
Each of these factors shaped our methodology and made a strong case for innovation.Â
Â
The Robotics-First ApproachÂ
We engineered a bespoke demolition solution that centred on the Brokk 200 demolition robot, chosen for its remote capabilities, precision, and power-to-size ratio.Â
Here’s how we brought it to life:Â
- Custom Engineered Platform: Our in-house team designed and fabricated a steel platform to support the Brokk 200. It was craned into position and suspended just above the stack, reducing wind impact and structural load.Â
- Safe, Remote Operation: The robot was operated from the ground, removing people from high risk zones and allowing demolition to continue during night shifts and high-heat conditions.Â
- High Precision Dismantling: Working from the outside ininside out, the robot provided controlled demolition, removing risk to adjacent structures and enabling real time adaptation during the works.Â
This wasn’t off-the-shelf thinking, it was a solution designed specifically for the site, the season, and the stacks.Â
Â
Innovation Backed by ExecutionÂ
While the methodoloy chosen, the Brokk 200 robot was a standout feature, the success of the project came from the strength of every detail – —precise planning, skilled execution, and integrated systems all working in unison. We:Â
- Planned for everything – including cyclones and supply delays, with spares and contingency equipment onsite.Â
- Selected skilled operators – calm under pressure, with strong communication to overcome distance and night time visibility challenges.Â
- Protected operating assets – constructing a bespoke scaffolding deck to safeguard the live boiler house throughout demolition.Â
- Managed waste differently – working within tight confines to remove debris without traditional stockpiling methods.Â
All of this contributed to early completion, zero damage, and zero safety incidents.Â
Â
We don’t pursue robotics or emerging tech for the sake of innovation. When the project environment demands it, like working 70 metres in the air, next to a live plant, we bring smart thinking, the right tools, and deep industry experience to the table.Â
The Kalamia Sugar Mill project is proof of what’s possible when bold ideas meet precise execution.Â
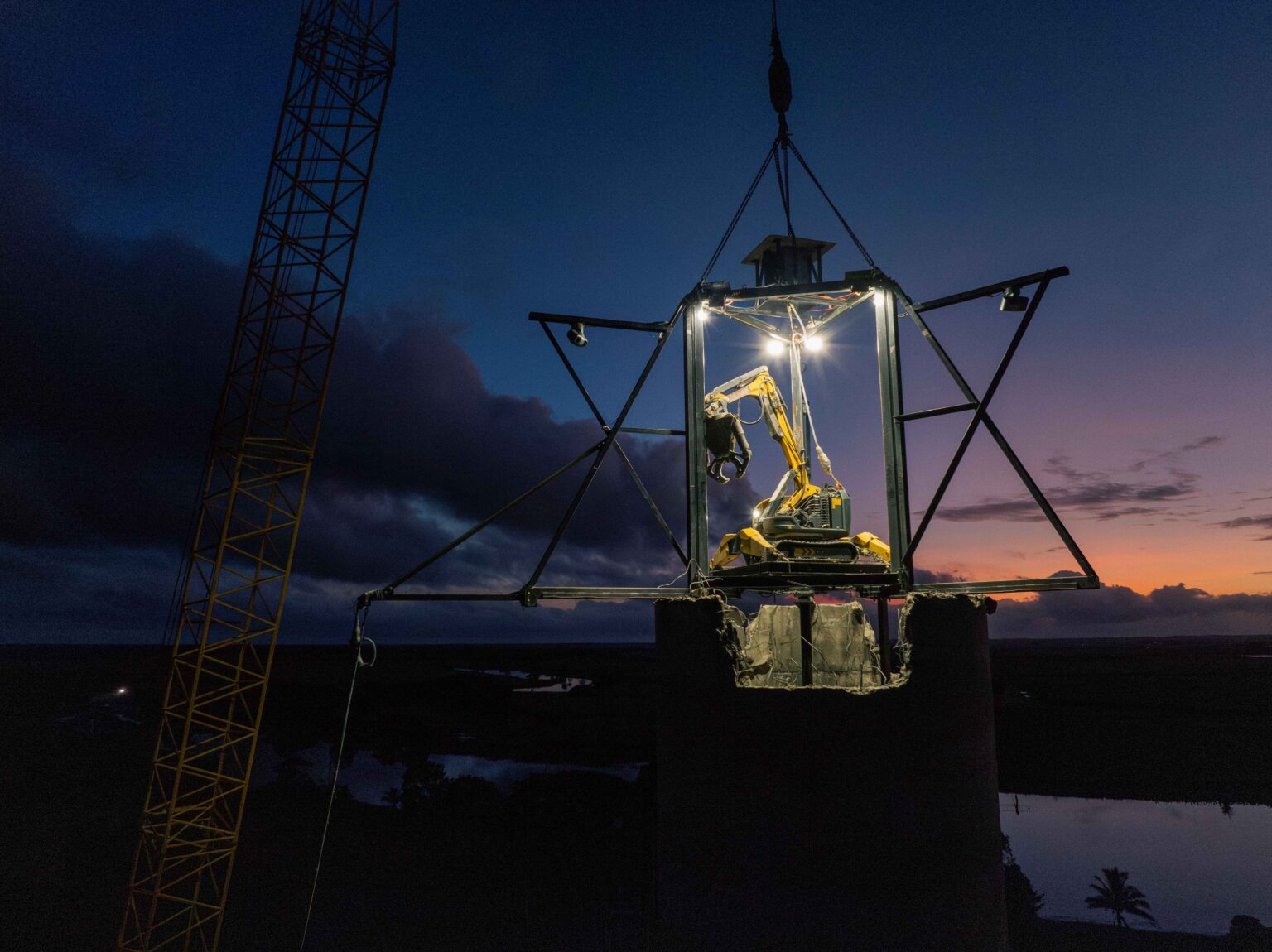